Fabriquant déjà des visières destinées aux personnels soignants depuis le début du confinement, au moyen d'imprimantes 3D, le laboratoire s'est lancé dans la production par injection de serre-têt de visière à partir de la mi-avril. Ceci s'est effectué sur la presse à injection DK CODIM 175 du Centre de Ressources Mise en Oeuvre des Polymères.
Cette action a donné lieu à un "white paper" écrit par les différents acteurs, et retraçant cette aventure :
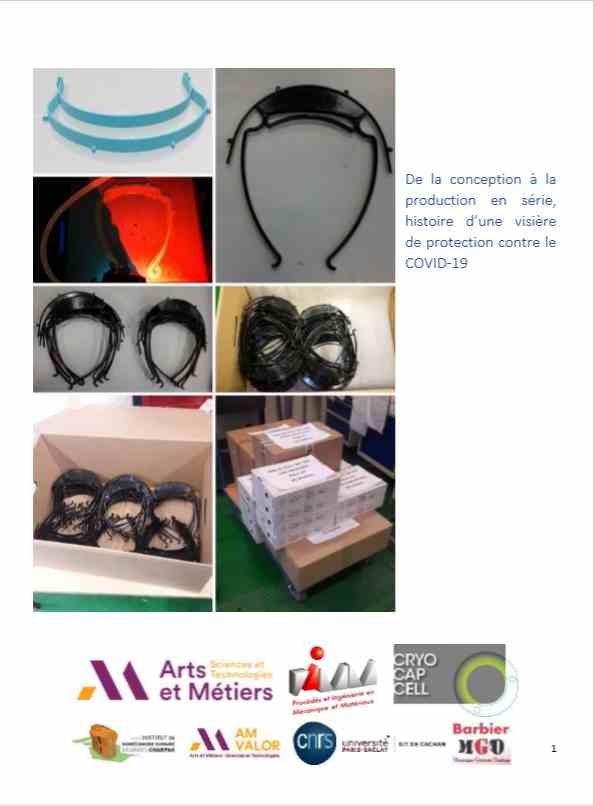
La fabrication par injection a été possible en utilisant:
- un moule prêté par l’IUT Cachan pendant la semaine de fermeture de celui-ci (du 13 au 20 avril 2020),
-
un moule mis au point et fabriqué par le laboratoire Pimm en collaboration avec la société CryocapCell hébergée sur le Campus. Le design de la visière a été modifié en tenant compte des retours des utilisateurs. Le moule a été conçu avec éjecteurs si bien que la cadence de production s'est largement accrue (une visière produite toutes les 30 secondes !!!). Le modèle géométrique de la visière est téléchargeable ci-dessous, celui du moule pour sa reproduction est disponible sur demande à contact@cryocapcell.com
Le modèle géométrique de la visière est disponible sur demande à pimm-contact@ensam.eu, celui du moule pour sa reproduction est disponible sur demande à contact@cryocapcell.com .
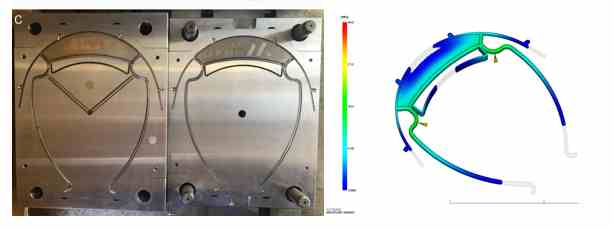
La production a ainsi pu démarrer grâce à la participation de nombreux membres volontaires du laboratoire : pour chaque demi-journée, une équipe a été constituée d'un expert Injection et de deux membres pour les opérations de décarottage, d’ébavurage et du conditionnement des visières mais également de la préparation des feuilles des visières qui nécessitent un perçage de 4 trous avec une perforeuse standard de reprographie...
Les matériaux utilisés ont été un copolymère PP-PE disponible au laboratoire, un polypropylène fourni par le Cnam, un polyamide ou du POM (Polyoxyméthylène) ... Les carottes et canaux d’alimentation (20% de la masse de la pièce) ainsi que les « mauvaises » pièces sont broyés localement et sont alors réutilisés pour la fabrication. Rechercher l’approvisionnement matière pour assurer la production (environ 25 kg par jour) a été une action très importante : qu'il s'agisse de granulés de matière pour l’injection ou des feuilles. Les équipes du Pimm ont pu compter sur leur partenaires : la société Arkema pour la fourniture de polyamide en cours ainsi que Wipak et Toray Films Europe qui leur ont fourni des bobines de films de PET adaptées à l’application; près de 800 mètres de films pour chacun permettant de préparer plus de 3 500 feuilles. Des fournisseurs de papeterie, d'élastiques ont aussi été de la partie !!!
Très beau bilan : 2000 pièces la première semaine avec le moule sans éjecteurs, puis environ 3500 pièces par semaine avec le second moule. D'ici la fin du mois de mai (date à laquelle cette action s'achèvera pour reprendre nos missions) la production aura dépassé les 10 000 pièces.
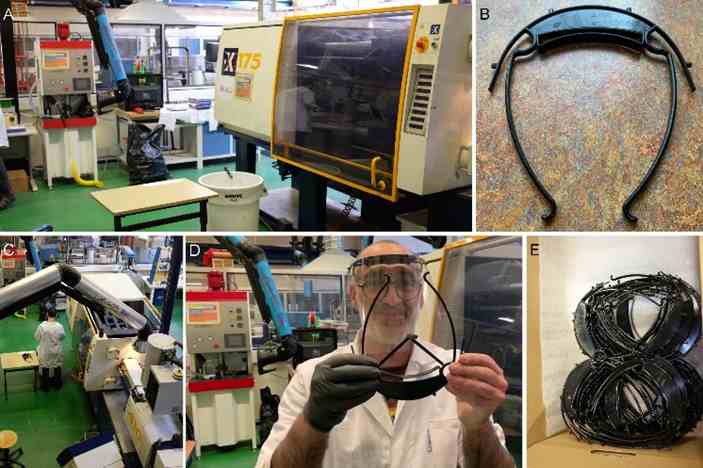
A- Machine d’injection du PIMM des Arts et Métiers. B- Serre-tête injecté en PA6
C- Séance de production par les équipes de recherche du PIMM. D- Masque posé sur le visage. E- Production horaire de visière.