Please contact Etienne Balmès (etienne.balmes@ensam.eu) and Léo Morin (leo.morin@ensam.eu) for more details
Context and Challenges
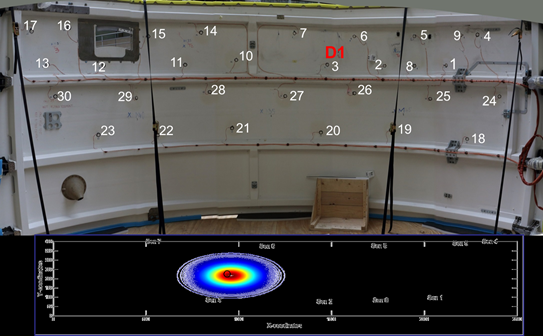
Mechanical waves propagating in a structure or a material interact with the interfaces present in volume or at their boundaries. The interfaces in the case of structures are contacts between mechanical parts whereas in a material, they characterize the microstructural heterogeneity. At an interface, the waves are partly reflected, partly transmitted. These effects lead to structured waves in the medium which locally can induce states of tensile stress. If this state of stress is sufficiently high, it leads to a damage of the medium: decohesion of the interface and initiation of porosity. The loaded interfaces can themselves re-structure the mechanical waves through the medium to a scale of the material or structure. This modification of wave structures is used to detect defects in the context of the health monitoring of components.
Specific features at PIMM
The Laser research group has been working on Laser Shock for a long time with two applications: Laser Shock Peening and Laser Shock Adhesion Test. Thanks to the Shock Laser platform, the laser research group is now able to produce damage at specific locations in the microstructure to test the adhesion of interfaces or create controlled damage. In addition, the P&C research group is studying the damage of laminated long-fiber composites during high speed dynamic loading. The Comet research group uses an ultrasonic fatigue machine to study fatigue at very large numbers of cycles. Lastly, the Dysco research group has been working on long-time vibration phenomena and their interactions with non linear contacts as well as on the detection of defects by analysis of the wave structure. In all these studies, it is necessary to know the stress state to go back to the conditions of initiation and development of the damage. The associated dissipative phenomena are also the object of study when one is interested in the energy dissipated in fatigue or to reduce the vibrations in transport. This inter research group project therefore reflects PIMM's desire to share common tools for modeling and numerical simulation in order to better understand the dynamic effects in the presence of interfaces to access damage and energy dissipation. From an experimental point of view, the PIMM has mechanical testing machines to vary the strain rate in a wide range: quasi-static machine (strain rate <1 s-1), very high speed machine (1 s-1 < strain rate <100 s-1), Hopkinson bars (100 s -1 < strain rate <1000 s-1), laser shock (105 s-1 < strain rate).
Scientific issues
PIMM Lab addresses the following scientific questions:
• How to predict the stress state in non elastic media with mechanical waves and its change as a function of the medium damage ?
• How to model the wave structure changes and use them to detect defects ?
Some collaborative projects
2015-2018 FUI COMPOCHOC
2018-2022 ANR GIGADEF
2017-2020 ANR MONARQUE
2018-2013 H2020 REMAP
Industrial Partners : AIRBUS, PEUGEOT, SNCF, THALES, ...