From the beginning of the lockdown, our lab was manufacturing face-shields for nursing staff, using 3D printers. Mid-April, the manufacturing of headbands for faceshields with injection moulding began. The process was carried out on the DK CODIM 175 injection moulding machine belonging to the Polymer processing Ressource Center.
This action gave rise to a "white paper" written by the different actors, and recounting the adventure:
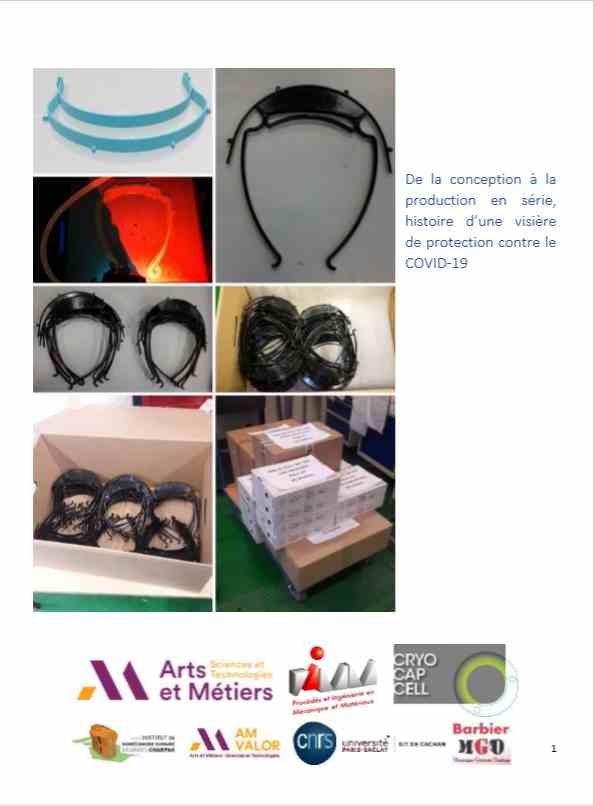
Injection manufacturing was made possible thanks to:
- a mould lent by IUT Cachan during its closing week (from 13 to 20 April 2020),
-
a mould designed and made by the PIMM lab in collaboration with the company CryocapCell that is accomodated on Campus. The face-shields design was adjusted according to users feedback. The mould has been designed with ejectors so that the production rate has significantly increased (one face-shield produced every 30 seconds!). The geometrical model of the headband is available on demand at pimm-contact@ensam.eu. The mould design is also available on demand (please send an email to contact@cryocapcell.com).
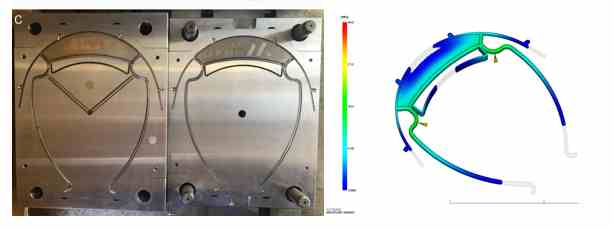
Thus, production could start thanks to the participation of many voluntary members of the laboratory: for each half-day, a team was made up of one Injection expert and two members for the operations of deburring and packaging of face-shields as well as for the preparation of the sheets which require a drilling of 4 holes with a standard paper perforatring tool.
Materials used were: a PP-PE copolymer available in the laboratory, a polypropylene supplied by the Cnam, and a polyamide or POM (Polyoxymethylene). Sprues and feed channels (20% of the mass of the part) as well as "bad" parts were locally crushed and are then reused for manufacturing. Searching for the material supply to ensure production (about 25 kg per day) was a very important action: whether it was sheets or granulated material for injection. The PIMM teams could count on their partners: Arkema supplied polyamide, and Wipak and Toray Films Europe have given reels of PET film fitting for use (almost 800m of film each, enabling us to prepare mort than 3500 sheets). Suppliers of stationery and rubber bands were also involved!
Very good results: 2000 pieces the first week with the mould without ejectors, then about 3500 pieces per week with the second mould. By the end of May (date on which this action was entend to resume our usual missions) production has exceeded 10,000 parts.
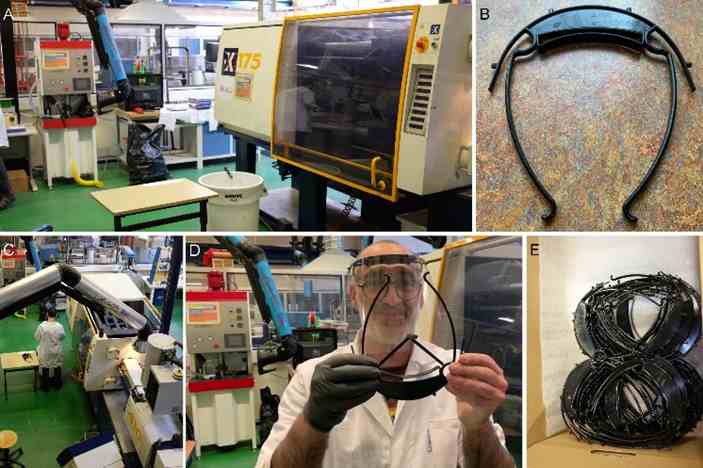
A- Injection machine from PIMM, Arts et Métiers. B- Headband injected in PA6
C- PIMM.research teams during a production session. D- Face-shield worn. E- Hourly face-shields production.