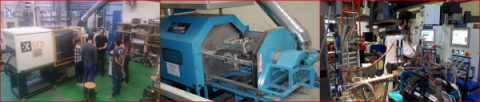
The processing of plastics includes the processes of transforming polymers into finished or semi-finished products.
The Implementation Resource Centre (centre de mise en oeuvre) pools our equipment on the Pimm site and on the Pimm-Cnam TP platform and provides an innovative machine park (reactive and multilayer rotomolding, multilayer extrusion or micro-injection for example) for the Polymers and Composite research group.
Today, the resources at our disposal, some of which are quasi-industrial, cover a very wide range of techniques used in this field: injection, rotomoulding, extrusion, thermoforming, and even additive polymer manufacturing.
Injection
We are developing research around the thermoplastic injection moulding process, in particular on the prediction of shrinkage and deformation, on the properties induced by flux welding lines, on the addition of fillers to improve mechanical or electrical properties. Most of our molds are instrumented in pressure, temperature and heat flow. We rely on a dialogue between experimental measurements and results from simulation code to answer the problems raised.
In addition, we provide services for manufacturers in the field of thermoplastic injection moulding. Our latest achievements concern the manufacture of moulded conductive electrodes for DREEM / RYTHM and high temperature transparent motorcycle housings for EMD / ESTEVES Motocycles Design.
(Click on the title if you wish to know more about our equipment)
Rotational moulding
Rotational moulding, whether reactive or by melt, is an implementation technique that makes it possible to obtain parts that are generally hollow, of various volumes and shapes. Rotational moulded products are used in many sectors such as equipment, boating, outdoor toy industry, automotive...
As such, for more than twenty years the Pimm and its teams of researchers and technicians have been developing a strong expertise in automotive tanks for storing hydrogen at very high pressure, as well as the design and manufacture of turbomachines that were, until now, carried out by other processes. For rotational moulding, there is very little limit to the production of high value-added parts, from very large to very small volumes.
(Click on the title if you wish to know more about our equipment)
Extrusion
(Click on the title if you wish to know more about our equipment)
Thermoforming
(Click on the title if you wish to know more about our equipment)
Additive manufacturing
Additive manufacturing by molten wire deposition is an implementation technique that makes it possible to obtain parts with complex geometry without molding or machining, by accumulation of molten polymer strata. The mobile extrusion head follows a digitally controlled manufacturing process from a spatial partition layer by layer obtained through the processing of a CAD file.
(Click on the title if you wish to know more about our equipment)
Compression
(Click on the title if you wish to know more about our equipment)
Corona treatment
A Corona treatment device (10cm wide) allows a surface treatment of polymers in order to modify their surface energy. This allows a good coating of aqueous solutions on hydrophobic surfaces such as polyolefins. This can be done, for example, on our extrusion films.
Film application: barcoaters
(Click on the title if you wish to know more about our equipment)