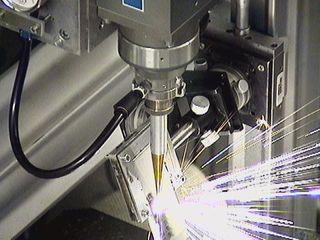
Since it was first invented 50 years ago, and the early industrial developments in the 80s, laser has progressively reached maturity in the field of materials processing. It is a unique tool able to remove material by cutting or drilling, weld thicknesses up to several centimeters, manufacture complex parts by powder melting, and harden or texture surfaces to micrometre or millimetre scale for instance.
The mastery of those processes implies:
- A deep understanding of physical processes at stake in the different regimina of interaction between laser and material, acquired thourgh relevant and various experimental diagnostics (high speed cameras, IR thermal camera, Doppler velocimetry, spectroscopy…);
- The implementation of more or less simplified numerical modelling or simulations;
- A study of the residual states of materials: appearance, topography, microstructure, and mechanical state, in order to correlate these states with the thermal, thermo-hydraulic and thermo-mechanical cycles locally experienced by the material.
The LASER team from the PIMM lab has therefore a twofold purpose: (1) understand and improve the implementation of laser processes, and (2) understand the effects induced in the (often metallic) material. All of this necessarily involves the use of recent and appropriate laser sources or machines, such as in 2013 (Purchase of a new Nd:YAG impulse shock generating laser as part of SESAME Hephaistos), or in 2016 (Purchase of the SLM125 HL Additive Manufacturing machine through ERDF co-financing).